A Critical Step in Automotive Manufacturing
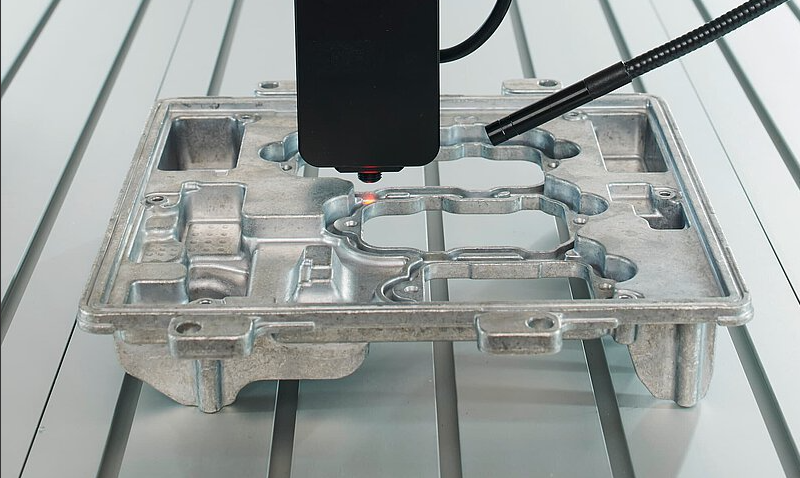
In modern automotive manufacturing, aluminum die-cast housings are indispensable components used across numerous applications—including engine control units, autonomous driving electronics, power electronics for hybrid and electric vehicles, as well as pumps, motors, and transmission systems. These housings typically consist of two joined parts sealed using liquid adhesives to ensure resistance against environmental influences and fluid ingress.
The reliability of these adhesive bonds is highly dependent on surface cleanliness, especially in the sealing groove area. During die casting, mold release agents are essential to ensure smooth part ejection, and subsequent machining introduces cooling lubricants. Residual contamination from either source can significantly impair adhesion, compromising both seal integrity and product performance.
Non-Destructive Cleanliness Testing Using Fluorescence Measurement
To ensure robust bonding performance, manufacturers must verify that surfaces are sufficiently clean prior to adhesive application. Fluorescence-based measurement has emerged as an effective, non-destructive technique for assessing surface cleanliness—particularly in the critical sealing grooves of die-cast aluminum housings.
This method enables operators to detect trace residues of organic contaminants, such as release agents and lubricants, that would otherwise go unnoticed with conventional visual inspection. Real-world applications show that deeper and more complex geometries—such as those found in sealing grooves—pose greater cleaning challenges. These areas also tend to accumulate more release agent, exacerbating contamination risk.
By conducting high-resolution, point-by-point fluorescence measurements directly on the functional bonding surfaces, manufacturers can establish confidence in the cleanliness of each component. Furthermore, process-specific cleanliness thresholds can be defined based on empirical performance data or correlation with destructive tests, such as tensile pull-off tests. These thresholds provide a valuable benchmark for in-process quality control.
Shop Floor Ready Portable Instrumentation
The SITA CleanoSpector, a handheld fluorescence measurement system, has proven to be a reliable solution for cleanliness inspection. Its portability makes it ideal for use across multiple stages of production—from pilot runs and process setup to random sampling during full-scale manufacturing.
By enabling quick, repeatable checks on the shop floor, this technology supports robust process control strategies aligned with industry quality standards. Its application directly supports the reduction of defects, the assurance of bonded joint integrity, and the overall improvement of product lifecycle performance in advanced automotive systems.