If you work in gas and steam turbine maintenance or assembly, you may have heard about iMAP. It’s a system that is increasingly being used to improve product quality whilst also introducing significant time savings. Let’s take a little time to explore the ways it does this.
What does it do?
First, let’s cover the basics. iMAP stands for Integrated Measurement and Assembly Platform. This is a pretty accurate description of the system. The system is built around a precision RPI rotary table. The system can be specified with a variety of table sizes up to 1,200mm (47”) diameter with a maximum supported load capacity of up to 14 tons (28,000 lbs) with a variety of smaller sizes also available to suit varying sizes of rotors.
Flanking the table are a series of touch probes. These come in contact with the part placed on the system, allowing measurement of Roundness, Eccentricity, Diametral Runout, Planar Runout, Circular Flatness and Parallelism. If you’re not familiar with some of these metrology terms, you can check out a glossary here.
In addition, it’s also possible to specify the innovative Intellistack software which is a predictive system to help correctly align turbine stages. This allows vibration and imbalance to be minimised.
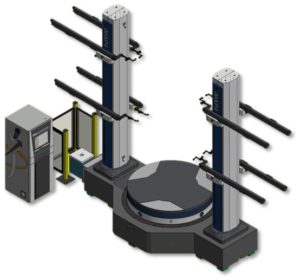
How does it work?
The underlying principle behind iMAP is simple. When a rotor stage is placed onto the system, the probes are aligned with the part and the system is ready to go. The table is then rotated (a process that can be specified either manually or motor driven). The probes collect geometric data in realtime during rotation, collecting 3,600 measurement points in one revolution.
As stages are added, these are also measured. This creates a detailed picture of the geometric makeup of the rotor as it is assembled (or reassembled).
How does Intellistack impact turbine performance?
Earlier, we touched on the concept the Intellistack software. This adds a valuable extra dimension to all of this already useful geometric data. Intellistack takes the measurement data that iMAP has collected and use it to predictively suggest the best way to assemble the rotor.
We all know that there is no such thing as a “perfect” part – there will always be at least some deviation from nominal values. These deviations introduce imbalance and vibration into an operating turbine which reduces efficiency. Intellistack does something pretty smart to minimize the problem. It determines the geometric deviation in each stage. Using this data, it suggests the optimal positioning each. It them informs the operator how by many bolt holes each rotor stage should be rotated for optimal alignment.
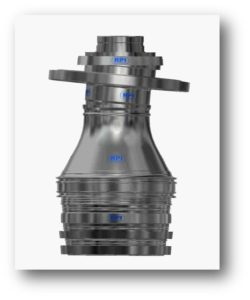
Productivity – the big benefit
All of this clever technology clearly helps build a better product. Additionally, huge amounts of time are saved by metrology work being conducted in situ at the point of assembly so the rotor no longer has to be taken elsewhere for measurement. And in the case of using Intellistack, you know that the vibration performance will be optimal before even running the turbine up to speed.
That means a dramatic improvement in throughput for assembly and reassembly – and that represents real value. In fact, tests conducted have shown that time savings over alternative approaches are up to 90%!
It’s a serious time saving which is not the only benefit. Impressively, iMAP has also shown repeatability performance that is more than 5 times greater than manual methods at the same time.
It’s no surprise that iMAP is proving so popular in both turbine assembly and maintenance, the benefits are hard to ignore. There’s more data available on iMAP here and you can see a video of it in operation here.