Making sure that the areas of metrology we work in are easy to understand is a huge passion of mine. I also believe it’s vital in creating a healthy future for the sector. Here’s why.
Starting at the Beginning
I joined the metrology community back in mid-2004. Before then, my familiarity with metrology was limited, to say the least. In fact, I had moved into the industry with a background in networking and IT infrastructure. I’d joined a then tiny start up called Third Dimension, which had just invented a new-fangled laser measurement system called GapGun.
Initially my primary role was training customers, installing the equipment, writing manuals and so on. These were relatively early days of embedded computing, so my technical background was useful – especially given that the product was very early into its lifecycle.
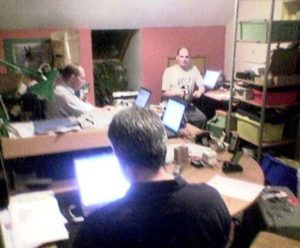
What I was missing, though, was a great deal of knowledge about metrology. To add to that, the principles used in the product were both niche and, in some cases, new (particularly, how to define a measurement on a very specific type of freeform surface).
Getting into the lingo
Within a week, I was in California to assist the company’s new distributor perform product demonstrations at the excellent CMSC conference. It’s fair to say that was a baptism of fire! But it was also a tremendous learning experience. Whilst there, I learnt about the existence of a whole host of 3D measurement systems that were previously alien to me: Laser trackers, portable arms, white light scanners. This fascinated and inspired me in equal measure.
I took something from finding out about each of these beyond their underlying complexity from a product functionality perspective. It was that the application of the technology was, in all cases, at least as important as the measurement device itself. This was the beginning of a lifelong journey of learning that continues to this day.
Very quickly I learned that whilst a great deal of concepts and terms within the industry were common across multiple applications and equipment types, an equal amount weren’t.
What about everone else?
I started to wonder about something. Did this lexicon of specific functions and terms make sense to all the customers I’d be talking to? I very rapidly discovered the answer: No. As I look back, I realize the answer was obvious. This was new technology, a new approach and in some instances new terminology.
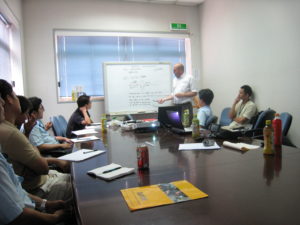
I was reminded of a time when, as a young apprentice entering the world of work, I was given some advice. Never assume the person you are talking to understands the same terms as you do. This was that advice incarnate. And so, I made a point to try and make the areas I was working in as straightforward as I could.
Complex Products Require Greater Engineering Skills
As humans, we build some clever stuff. Our buildings are ever taller, our consumer electronics more complex, our airplanes more efficient, our cars more reliable. Look back several decades and consider the difference we see today.
As we make our products better, the mechanisms by which we do it become more complex, too. Algorithms are dramatically more advanced. Quality control mechanisms are more encompassing. Tolerances become tighter. All of this comes about thanks to increasingly smart engineering. There’s a challenge here though, too. As we push the boundaries of what we know to be possible, we continue to need skilled engineers to enable all of this to happen.
Are there obstacles for us further down the road?
This has the potential to become a problem for engineering. In 2016, the OECD reported that in the USA, 40% of companies were facing a skills shortage (with Canada and Mexico reporting 34% and 44%, respectively).

That’s compounded by a second issue: Our aging population. By 2050, it’s estimated that the population at retirement age will have doubled in size. That should make us even more aware of the need to encourage future generations into the industry.
With a limited labor pool, there is always going to be competition to attract bright young talent. It seems logical then, that breaking down as many barriers as possible to attract new entrants is not only sensible… it’s necessary.
Not All People Using Metrology are Metrologists
For those of us that use metrology equipment every day, it’s easy to forget that most people that use metrology aren’t metrologists. They’re engineers and technicians that require it to do their jobs.
Let’s think about that in the context of my experiences in metrology as a young engineer joining the industry (and possibly yours, too). Metrology has a lot of technical terms. Some are specific to certain types of equipment, some are more universal. Either way, they are often extremely niche.
Are we always focussing on our core roles?
Every day, every single one of us undoubtedly has more work than we really have time to do. It’s the nature of the beast. That being the case, does inundating our co-workers, suppliers, customers, and peers with excess niche technical terminology that they’ll at best need to spend a second thinking about and at worst go and learn, really make sense?
I suggest it doesn’t. Rather, we should be using our finite time and energy to work together to solve problems and improve the products, processes and activities that are central to our remit.
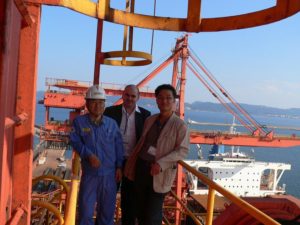
Let’s Affect Positive Change
These combined factors are important not just to our sector but to engineering, manufacturing and research in its entirety. We will need metrology skills increasingly as time goes on.
At the same time these extra skills are needed, our workforce will come under increasing pressure from retirements and the need for new blood. We must make careers in our sector compelling. Increasing accessibility to new entrants is a massive step in the right direction.
At Wyvern, we’ve made it a core part of our mission to ensure our work, our solutions, and our data as easy to understand as possible. I strongly encourage you to do likewise. I can see nothing but benefits.
John Kane is President of Wyvern. You can view his LinkedIn profile here.