When working with circular components, considering runout is important. Runout is error introduced into roundness conditions caused by, and expressed, in different ways. One of these is planar runout.
In this post, we’ll explore what planar runout is and why understanding it is important.
Planar runout is the effect of a surface at one end of the axis of rotation on a circular part deviating in its position from normal for some reason. In an ideal world, parts would be perfectly manufactured and there would be no error. Of course, here in the real world, that doesn’t happen. Instead, various factors influence the variation introduced into a part.
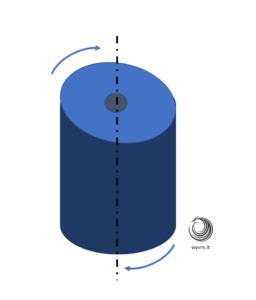
Imagine a cylinder with a flat top mounted centrally on a rotary table (error introduced by the part not being central can be observed in our post about diametral runout). In this real-world part, that top won’t be completely normal to the axis. In other words, it is varying from a theoretical deviation of zero. For example, there could be a washer (or any other foreign object) underneath one corner of the cylinder, or the top surface could be incorrectly finished.
In both cases, the effect on planar runout would be the same: There would be a variation on the surface that would be expressed in a way that would look like a rhythmic undulation if we were to measure. Think of a warped vinyl record on playing on a record player. If you watch the stylus of the player on the surface of the record as it plays, it is moving up and down. This is similar to what the effect of planar runout looks like.
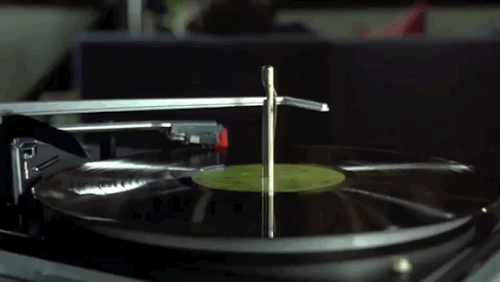
Whilst the axis of rotation won’t necessarily be vertical like in the analogy above, the same principle also applies if you shift the plane of the rotational axis to horizontal, for example.
If this planar surface joins with another part (for example in the stack of a turbine), it can cause imperfections in rotation which impact all the other parts in the assembly. This can cause balance and vibration issues and can make error causes much harder to track down once the assembly is complete. That means it’s important to measure and identify it as early in the process as possible.
iMAP, GeoSpin and GeoInspec can quickly and easily measure these conditions and help eliminate and out of tolerance conditions without taking parts from the shop floor.
If you’d like more information on runout or any of the other geometric conditions we measure, don’t hesitate to contact us. We’re always happy to talk circular geometry!