The automotive industry relies on uncompromising precision, efficiency, and reliability.

Automotive
The automotive industry operates at the intersection of high-volume production and precision engineering. Daily, automotive manufacturers navigate a range of challenges to maintain efficiency, meet stringent quality standards, and stay competitive. We understand these complexities and tailors its precision measurement solutions to address the unique challenges that manufacturers face on the shop floor.
Day-to-Day Challenges in the Automotive Industry
Meeting Precision and Quality Standards
Automotive components, from engine parts to brake systems, must adhere to exacting standards to ensure safety, performance, and durability. Variations in geometry, runout, or concentricity can result in parts that underperform, impacting everything from fuel efficiency to safety.
Minimizing Production Downtime
With strict production schedules, even minor interruptions can disrupt workflows, cause bottlenecks, and lead to significant revenue losses. Equipment setup time, measurement inaccuracies, or equipment malfunctions are common contributors to downtime.
Ensuring Consistency in High-Volume Production
In high-volume manufacturing, consistency is essential to avoid costly rework or product recalls. Variability across production batches can result from machine wear, environmental factors, or operator error.
Adapting to New Technologies and Design Changes
As automotive technology evolves, manufacturers frequently face changes in design, materials, and production processes, particularly with the rise of electric vehicles. Adapting inspection processes to accommodate new specifications can be time-consuming and costly.
Maintaining Compliance with Industry Regulations
Automotive manufacturers must comply with a range of safety, environmental, and performance regulations. Compliance requires rigorous quality checks to verify that components meet regulatory standards, which can strain resources and extend production times.
Managing Costs and Maximizing Efficiency
Balancing quality with cost-efficiency is a constant challenge in automotive manufacturing. Manufacturers are under pressure to reduce waste, optimize resource allocation, and minimize labor costs without compromising on quality.
At Wyvern, we deliver high-performance rotary measurement and positioning solutions that streamline manufacturing and inspection processes, supporting automotive companies in achieving outstanding quality control and production efficiency. Our products are built to handle the exacting requirements of automotive applications, providing the accuracy needed to meet and exceed industry standards.
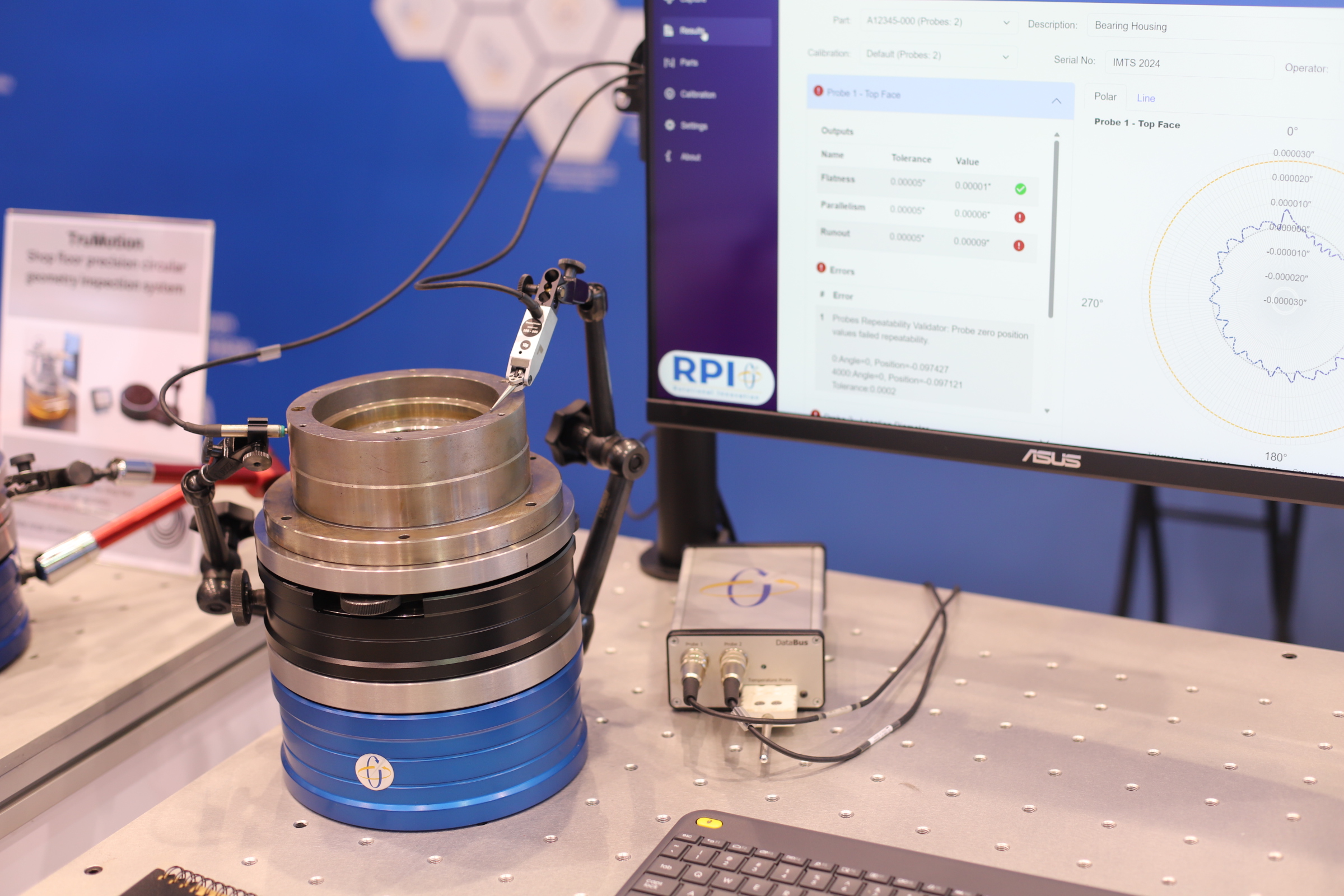
Automotive customers use our equipment in a wide range of ways, including using our range of technical cleanliness systems for Quality and Inspection, increasing CMM throughput with the Quadrant range, and sensor testing and positioning using the LabStandard precision rotary table.
Our range includes specific products designed to meet the diverse needs of the automotive industry:
- LabStandard Rotary Tables: The LabStandard series delivers reliable, high-precision performance with incredible stability. Perfect for inspecting gears, shafts, and other rotational components, the LabStandard ensures minimal runout and superior repeatability.
- TruMotion Rotary Tables: For applications requiring ultra-smooth rotation, TruMotion offers exceptional control through air bearing technology. This product is ideal for brake system components and other parts where stability and minimal friction are essential.
- Quadrant Rotary Tables: Designed to increase the capability of Coordinate Measuring Machines (CMMs), Quadrant rotary tables extend the reach of CMM inspections, enabling automotive manufacturers to inspect larger parts with shorter cycle times and greater flexibility.
Want to know more?
We're always happy to discuss your requirements, potential applications and talk through concepts to help improve productivity and quality